Roller chains are an essential component of industrial power transmission systems. They have been in use for over a century and have proven to be one of the most reliable means of transferring power between different machine sections or between the power source and the machine itself.
Brief History
Hans Renold invented the first roller chain in 1880. He came up with the idea while studying bicycle chains. The initial design consisted of a series of metal cylinders connected by pins, which allowed for the smooth transfer of power.
Over time, they made improvements to the design, such as adding side plates and using different materials. Today’s roller chains are much more advanced and have become an integral part of various industries.
Structure
Roller chains have a simple yet effective structure. They consist of inner and outer plates, pins, rollers, and bushings. The internal components are usually made of hardened steel or alloy steel to withstand the high tension and stress that comes with power transmission. These elements work together to transfer power from one machine to another.
Applications
Roller chains are widely used in many industries for power transmission purposes. They are commonly found in manufacturing plants, agriculture equipment, mining machinery, and even bicycles and motorcycles. These chains are used to transfer power from engines or motors to various machine parts, such as conveyor belts, gearboxes, and pumps.
Advantages
Roller chains offer several advantages that make them the preferred choice for industrial power transmission. First, they have a high load-carrying capacity, which means they can withstand heavy loads without breaking or wearing out
In mechanical power transmission, roller chains play an indispensable role. As the most commonly utilized chain drive, they are the heart of many domestic, industrial, and agricultural machines. Roller chains, composed of a series of cylindrical rollers connected by links, display an impressive balance between durability, efficiency, and versatility.
The roller chain’s design is ingeniously simple yet highly effective. Each chain operates by running on a rotating sprocket, which is powered by a motor, resulting in the chain’s movement. This alternating pattern of links enables the smooth transmission of power. Whether it’s the operation of heavy-duty machinery or ensuring seamless function in specialized areas, roller chains prove their worth time and again.
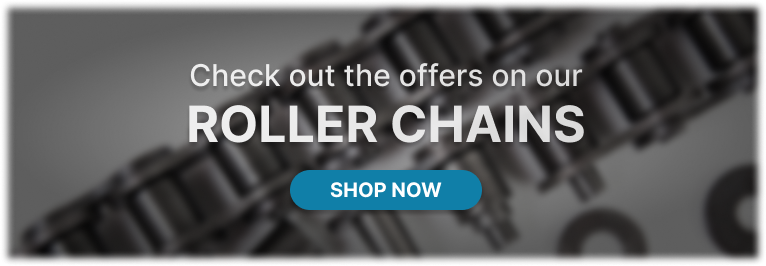
Types of Roller Chains and Materials Used in their Manufacture
There are various types of roller chains available, each tailored for specific applications aLastly, plastic chains, often made from durable, high-strength composites, are a good choice for lighter, less demanding applications. These chains offer the benefits of quiet operation, lighter weight and a lower cost, while still providing adequate strength for many tasks.
Another noteworthy type is the stainless steel roller chain, chosen explicitly for operations in corrosive environments, like food processing or chemical manufacturing, where regular chains would quickly degrade.
Then, there are the O-ring and X-ring chains, which feature a lubricated seal at each link, reducing wear and extending the chain’s lifespan. These chains are ideal for operations where durability and reduced maintenance are critical.
These types of roller chain serve a specific purpose, demonstrating the diversity and adaptability of this fundamental component of mechanical power transmission. They find the biggest use in dirt bikes and motocross applications.
Silent chains, also known as inverted tooth chains or toothed chains, are another type of power transmission chain. They differ from roller chains in their design and operation. Silent chains are composed of flat, tooth-shaped links that mesh with the sprocket’s teeth rather than rolling over them. This results in a quieter operation, hence the name ‘silent cnd environments. One common type is the single strand roller chain, which consists of one chain row and is most commonly used in various industries.
Its simplistic design is suitable for most standard applications, ensuring efficient power transmission. For heavier loads, there are multi-strand chains – double, triple, or even quadruple, each additional strand offers increased power and load capacity.
Roller chains are crafted from a variety of robust materials, each possessing distinctive properties that can accommodate different industrial requirements. Carbon steel is a prevalent choice because of its excellent strength, durability, and resistance to wear. This type of steel can handle high loads and severe operating conditions, making it ideal for heavy-duty applications.
Another frequently used material is alloy steel. This is a blend of several metals that typically includes nickel, molybdenum, chromium, or manganese. The alloying process enhances the material’s hardness, toughness, and ability to withstand fatigue, making it suitable for high-stress, high-speed operations.
Brass, while not as commonly used, can be found in certain roller chains. Its natural resistance to corrosion and excellent machinability make it ideal for applications in corrosive environments such as maritime or chemical industries.
The teeth’s engagement with the sprocket also provides more accurate positioning and timing, making silent chains highly suitable for applications that necessitate precision, such as car engines or industrial machinery. Furthermore, silent chains’ design allows for a high load capacity and efficient power transmission, despite their compact build.
Identifying Roller Chains – Nomenclature
Determining the right roller chain for a specific application is crucial to ensure efficient operation and longevity. Roller chains are generally identified by a three-part numbering system: the pitch, the strand quantity, and the chain length. The pitch refers to the distance between the centers of the pins in the chain, typically measured in inches or millimeters.
The strand quantity indicates the number of chain rows, with single, double, triple, and so forth representing one, two, three, or more rows respectively.
Finally, the chain length, usually listed in links, determines the total length of the chain. While specific lengths can be specified, more often they are purchased in bulk spools and cut to length using tools, called chain breakers, specifically designed for that purpose.
Understanding this identification system is essential for selecting the appropriate roller chain, whether for replacing a worn-out chain or equipping a new machine. It ensures compatibility with the respective machinery and optimal power transmission performance.
Installation and Alignment of Roller Chains
Proper installation of a roller chain is crucial to its performance and lifespan. The first step is to ensure that the sprockets are correctly aligned. Misaligned sprockets can cause premature wear and decreased efficiency, so checking alignment with a straightedge or laser tool is critical. Sprockets should be parallel, and the chain should line up straight from the drive to the driven sprocket.
Next, the chain should be threaded over the sprockets, making sure that any master links are installed so they can be easily identified and are easily accessed. Deflection, or the amount of sag in the chain, must be properly set. Too little deflection (over-tightening) can lead to excess wear on the chain and sprockets, while too much deflection (under-tightening) can cause the chain to jump off the sprocket. A good rule of thumb is that the chain should deflect approximately 1/120th of the center distance between the sprockets under moderate pressure.
Half-links, also known as offset links, are used to increase or decrease the chain’s length by a single pitch, allowing for better fit and tension adjustments. They’re useful where the chain’s length doesn’t exactly match the distance between the sprockets, ensuring a smoother operation.
Finally, after installation, make sure to adequately lubricate the chain to reduce friction and wear. Remember, regular inspection and maintenance can prolong the life of your roller chain, ensuring efficient power transmission in your machinery.
Installing roller chains requires a set of specific tools which ensure an efficient and safe installation process. These include a chain breaker tool for splitting and disconnecting the chain links, a chain puller for aiding in the tensioning of the chain, a straightedge or laser alignment tool to verify sprocket alignment, and the proper lubricant for reducing friction and wear.
Additionally, a master link pliers might be necessary for handling the master link. Utilizing these tools is essential as they help prevent improper installation and ensure the longevity and optimal performance of the roller chain. Missteps during installation could lead to premature wear, reduced efficiency, and potential failure of the roller chain.
Importance of Roller Chain Maintenance and Best Practices
The importance of roller chain maintenance can’t be overstated. Regular maintenance is critical to the optimal functioning and longevity of the roller chain. When maintained properly, you can alleviate wear and tear, maintain smooth operations, and prevent unexpected breakdowns which could lead to costly repairs or replacements.
One key aspect of roller chain maintenance is regular cleaning. Dirt and debris can get trapped in the chain, causing friction and contributing to accelerated wear. Therefore, chains should be cleaned periodically depending on the operating environment and extent of use. After cleaning, it’s essential to apply a suitable lubricant to reduce friction between the links and ensure smooth operation.
Scheduling regular inspections is another crucial practice. This involves checking for signs of wear such as elongation, cracked plates, or damaged rollers. Noticeable elongation of the chain or frequent adjustments could mean the chain is close to its wear limit and may need replacement. A roller chain wear gauge can be a handy tool for this purpose.
In addition to these steps, keeping a maintenance log is highly recommended. A log sheet serves to track the history of maintenance tasks, note down any changes observed, and record the dates for future inspections or replacements. This will help in identifying consistent issues or patterns, allowing for timely preventive actions and ensuring the roller chain’s efficient functioning.
Remember, proactive maintenance is far more cost-effective and less disruptive than reactive maintenance. By following these best practices, you can significantly enhance the lifespan and performance of your roller chains.
Conclusion: The Integral Role of Roller Chains in Power Transmission
To sum it up, roller chains play a pivotal role in power transmission, essential to numerous mechanical and industrial applications. Their design, identification, installation, alignment, maintenance, and best practices are all fundamental elements to ensure their optimal performance and longevity. Mastering these aspects, whether you’re dealing with silent chains or roller chains, is the key to efficient machinery operation and a smoother industrial process.
We hope that this comprehensive guide has provided valuable insights into roller chains. Don’t forget that keeping a proactive stance on maintenance can save you from costly repairs and downtime in the long run.
We invite you to explore the extensive range of roller chains and related tools available on the PGN Bearings website. Each product in our inventory is designed for durability and optimal performance, ensuring your machinery operates efficiently and effectively. To get started, visit our website.